Try to imagine a single day without plastics. That means no cell phone, no computer, no packaged foods, no driving a car, no using a pen or wearing tennis shoes. Plastics are ubiquitous in today’s society, and for good reason. They are functional, versatile, hygienic and low cost – and they are used so widely that it’s difficult to imagine living without them, even for a day.
So it’s no wonder that the use of plastics has increased twenty-fold over the last 50 years, and in 20 more that number is expected to double yet again. While plastics make our lives easier, they also present challenges related to waste, marine pollution, and sustainability, and that means we must strike a delicate balance between making use of this important material, producing it responsibly, and managing its end of life.
Enter the circular economy. By placing a greater focus on recycling plastics and keeping them in the economy rather than producing waste, we can begin to make progress on the challenges associated with plastics today. But as the recycled products market grows, companies will need to place a greater focus on their supply chain choices, too.
The Problem with the Take-Make-Waste Production Model
The way plastics have traditionally been produced relies on a linear take-make-waste model: producers take oil and gas from the earth, make plastic products from them, and then, often, these products are designed to be used just once. After their very short useful life, they’re discarded.
Although these single-use plastics serve a very good purpose, like keeping food safe from contamination, the result is problematic. Each year, it’s estimated more than 34 million metric tons of plastics are incinerated or end up in landfills in the U.S. and Canada. Another 8 million tons leak into the ocean each year, a number that is unfortunately rising. Research suggests that ocean plastic stocks have already reached 150 million tons. If things don’t change, by 2025 it’s estimated the ocean will contain one ton of plastics for every three tons of fish, and by 2050, plastics could outweigh fish altogether.
While the environmental costs of the linear production model are dire, it also has financial consequences. Plastics packaging is a prime example. Today, only 14% of all plastic packaging is collected for recycling after use, which results in a loss of $80 to $120 billion per year. A whopping 32% of plastic packaging escapes collection systems in the form of leakage. The downstream costs of this pollution plus the cost associated with greenhouse gas emissions from packaging production is estimated to be $40 billion annually.
Even though the linear model has been in place since plastics were invented, it doesn’t mean nothing has been done about the impact on the environment. In the past, efforts to address plastic waste and pollution have focused on waste management and environmental clean-ups. However, those efforts are no longer enough. According to Breaking the Plastic Wave, we must act now to move away from the linear model because waiting even just five years to act could result in an additional 80 million tons of plastic in the ocean between now and 2040. That’s equivalent to adding 13,000 plastic bottles per second for the next 20 years.
The Circular Economy and the Rise of Recycled Materials
The alternative to a linear economy is a circular economy, which focuses on designing out waste and pollution, keeping products and materials in use, and regenerating natural systems. In the circular economy, products are designed to be used – not used up. The circular economy takes every stage of a product’s journey into consideration, including before it reaches the customer and after, too. In the instance of packaging, in a circular economy it would be designed to be reused, recycled, or composted.
This systemic shift is intended to benefit individuals, organizations, and businesses large and small, both locally and globally. When designed properly, the circular economy benefits society, the environment, and the economy. Compared to today’s model, adopting a circular economy in the plastics industry could reduce the amount of plastics entering the ocean each year by 80%, generate savings of $200 billion per year, reduce greenhouse gas emissions by 25%, and create 700,000 net additional jobs by 2040.
Technology is assisting the shift to a circular economy. Technologies are already available to repurpose plastics into valuable materials, and advanced technology can solve for some of today’s hard-to-recycle materials, like medical waste and building materials. According to the Closed Loop Partners Advancing Circular Systems for Plastics & Packaging report, this growing technology field could yield a potential addressable market of $120 billion in the U.S. and Canada alone. As some of the world’s largest brands, retailers, and plastics manufacturers make commitments associated with plastics recycling, recycled and recyclable content, and recovery, the demand for these products is projected to grow to 5 to 7.5 million metric tons by 2030.
The Role of Transportation in the Circular Economy
Keeping products in the loop will yield significant benefits – but it will also have an impact on supply chains. When products are diverted from landfills more recycled products (or waste products headed for recycling) will need to be move between producers, consumers and recyclers. Looking at recycled plastic resin alone makes the impact to supply chains clear: Global demand is projected to be 77 million metric tons by 2030, which translates to 902,900 rail cars or 3.6 million trucks needed to meet the demand for this one product.
The choice companies make between these two modes is a big one. The reason is that trains are a far more environmentally responsible way to ship freight than trucks. On average, railroads are three to four times more fuel efficient than trucks on a ton-mile basis and can move one ton of freight more than 480 miles on a single gallon of fuel. Because of these factors, trains generate a carbon footprint up to 75% less than trucks.
Just how much could we reduce greenhouse gas emissions if we shipped the 77 million metric tons of recycled plastic resin projected for 2030 by rail instead of truck? For simplicity’s sake, let’s say plastic resin shipped by rail instead of truck from Dallas to Los Angeles. According to the Union Pacific Carbon Emission Estimator, choosing rail would reduce the carbon footprint by 5,657,610 metric tonnes.
That number becomes more significant when you consider it is equivalent to:
- The carbon removed by 1,205,071 acres of U.S. forests
- The carbon removed by 144,834,816 tree seedlings grown for 10 years
- Greenhouse gas emissions avoided by recycling 1,968,848 tons of waste instead of sending it to the landfill
The demand for recycled plastic resin is rising. As it does, it will be important for plastics producers, materials recovery facilities, recyclers, processors and manufacturers to use an environmentally responsible shipping mode to meet their sustainability targets. Transporting by rail throughout the circular economy — from waste collection, to recycling, manufacturing and consumer buying — offers the economies of scale needed to meet the growing demand.
Shipping by rail offers cost and safety benefits, too. Rail can lower logistics costs by carrying the same amount of cargo in one rail car as 3-4 trucks, thereby reducing logistics management and administrative burdens by having fewer resources to manage. On average, rail also offers a lower cost per ton mile than truck. According to DAT Freight & Analytics, spot market truck rates have risen 48% since last year, and truck rates are projected to increase by 30% year-over-year in 2021. This trend is likely to continue, making the savings rail offers more important than ever.
Safety is another big benefit of rail. Trucks are six times more likely to be involved in a fatal crash: According to the National Highway Traffic Safety Administration (NHTSA), in 2018 a total of 4,862 large-truck vehicles were involved in fatal crashes in the United States, while railroad fatalities totaled just 806 in that same year. When products are shipped by rail instead of truck, it reduces the impact to consumer safety by removing trucks from the nation’s highways.
Rail: The Missing Piece
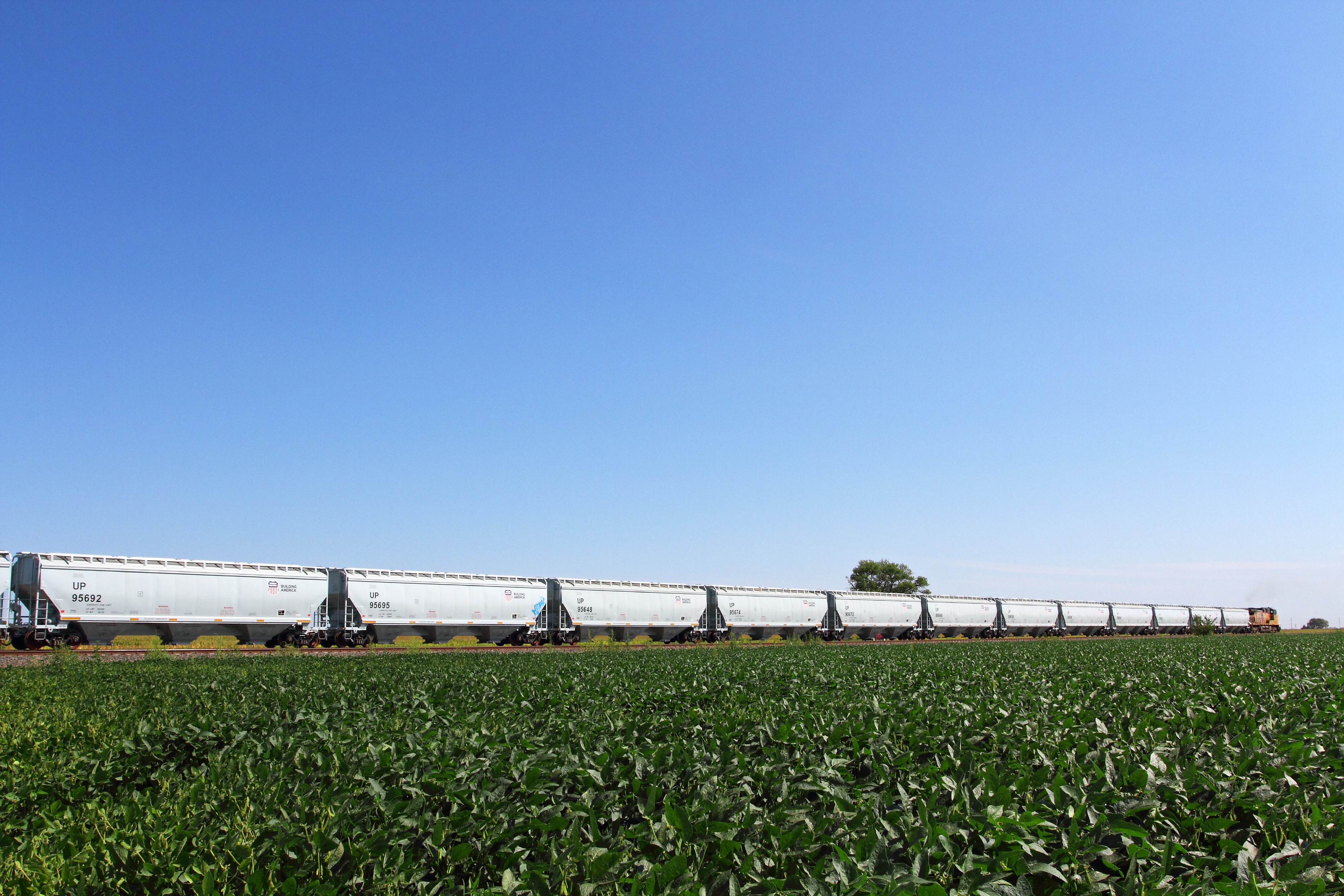
From a supply chain standpoint, rail offers the biggest sustainability return as more recycled products move through the circular economy. Fortunately, plastics producers already know the benefits of rail, and their plants are already set up to ship the vast majority of their resin by train. It stands to reason that the rest of the supply chain will need to follow suit in order to handle the magnitude of recycled plastics being shipped.
As new facilities inevitably pop up to serve the circular economy, it’s important for shippers of recycled plastics to consider rail from the beginning. Union Pacific’s team of experts can provide guidance and rail project management for businesses wanting to build, expand, or find a rail-served site. Completing the AccessUP questionnaire is the first step to get connected. Union Pacific also offers the Site Solutions Tool, which allows users to search from nearly 500 sites to locate a rail-served business. For a quick speed to market solution, Union Pacific Focus Sites are premier large-scale development areas with pre-approved rail designs.
Shipping truck after truck raises costs, complicates logistics, and has a larger carbon footprint. Choosing rail instead helps companies reduce their greenhouse gas emissions, lower costs, simplify their supply chain and make progress toward their sustainability targets. Adopting rail now will help shippers of all types be prepared for the surge in recycled products to come, while also reaping the near-term cost and safety benefits.
Questions About Rail?
If you have questions about shipping by rail, get in touch and we will connect you with a shipping expert.
Related Articles
- Rail: An Environmentally Responsible Way to Ship
- Plastics and Sustainability: How Dow and Braskem Are Working Toward a Greener Future
- Transportation: Delivering the Plastic Products You Can’t Live Without
- From Steam to Green: The Evolution of the Locomotive
- The Rail Industry Is Saving Millions of Gallons of Fuel a Year – And They’re Using “Cruise Control” to Do It
- Transportation Modes Revealed: A Comprehensive Look
- Rail 101 FAQs
- U.S. Freight Rail: The Envy of the World
- Quiz: Can Your Product Ship by Rail?